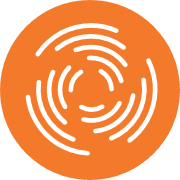
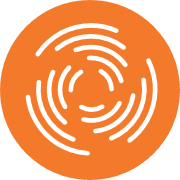
Tenders
Project identification number: GINOP_PLUSZ-1.1.2-21-2022-00070
Name of the beneficiary: Szeplast Zrt.
The title of the project: Export-oriented capacity expansion and product diversification, as well as further increasing the brand value of Szeplast Zrt. by bringing a new product line to foreign markets
Total cost of the project: 1 263 211 261 Ft
Subsidy amount: 631 605 630 Ft
Support intensity: 50 %
Place of implementation 6728 Szeged, Vass Mátyás út 5.
Actual project completion date: 2024. november
Project goal:
Expanding the production capacity of PVC granules, creating the necessary production capacity for the production of a new type of innovative plastic granule raw material product, developing the quality control equipment park, and developing the site’s infrastructure to reduce environmental impact.
The implementation of the project contributes to the strategic goal of Szeplast Zrt., to achieve an upper-middle class company size according to industry standards.
Project elements:
- Purchase of PVC extruder
- Acquisition of HFFR machine line
- Acquisition of trial extruder
- Acquisition of a test production line
- Development of measuring and dosing system
- Industry 4.0 system data collection system
- Obtain a colorimeter
- Obtain an LOI meter
- Development of electrical network
- Building a solar system
- Outdoor infrastructure development – Transformer station
- Construction of a fire alarm system
- Silo foundation
- Road construction
Cutting-edge technological solutions in the project:
Innovative raw materials: by building the HFFR granulate production line, the company can produce innovative raw materials that are important for the economy and meet the highest expectations and market standards. HFFR granulate (as a halogen-free and flame-retardant plastic material) provides a number of fire protection and safety features, primarily for cable manufacturers, which will become an increasingly common requirement of this segment in the future. With the implementation of the project, Hungary’s production capacity will be expanded with a product that is currently not available in our country, but as far as we know, no company in the neighboring countries has the production technology/capacity suitable for the production of HFFR granules in larger volumes. Both the equipment for expanding the capacity of the current PVC line and the machines in the new HFFR line are capable of producing high added value products and use the best technologies currently available in the industry. In addition to being able to produce economically, with little waste, and with accessible maintenance, these equipment are equipped with digital solutions that are suitable for the implementation of the Industry 4.0 production method. The company will take advantage of these features of the equipment, since the equipment will be operated in a common and integrated production control system, as it is now. Thanks to the computer-controlled automatic system, the main phases of production do not require human intervention: the measurement, preparation and mixing of the individual recipes and raw materials, as well as the extrusion and pelletizing, are controlled by the integrated digital system. The entire production process can be monitored and adjusted from the control center, and if necessary, based on the data provided by the sensors and other feedback devices, it is possible to intervene, interrupt or change the given production process, often without the physical intervention of the employees.
The Flowork Industry 4.0 software technology will be integrated within the framework of the project, which further strengthens the company’s commitment to Industry 4.0. With the Flowork Industry 4.0 solution, the collection of the necessary data becomes complete. By storing the generated data in a unified system, continuous quality control and tracking of products is possible. Although the current production units already have data collection functions, it is necessary to raise the analysis of the data generated by them and their feedback to inter-production quality control to an even higher level. This solution produces comprehensive, real-time data on all technological processes of the granulate production cycle. With their feedback, it supports the immediate solution or elimination of problems that arose during production. The system to be introduced enables the monitoring of more than 300 measurement points in the area of production.
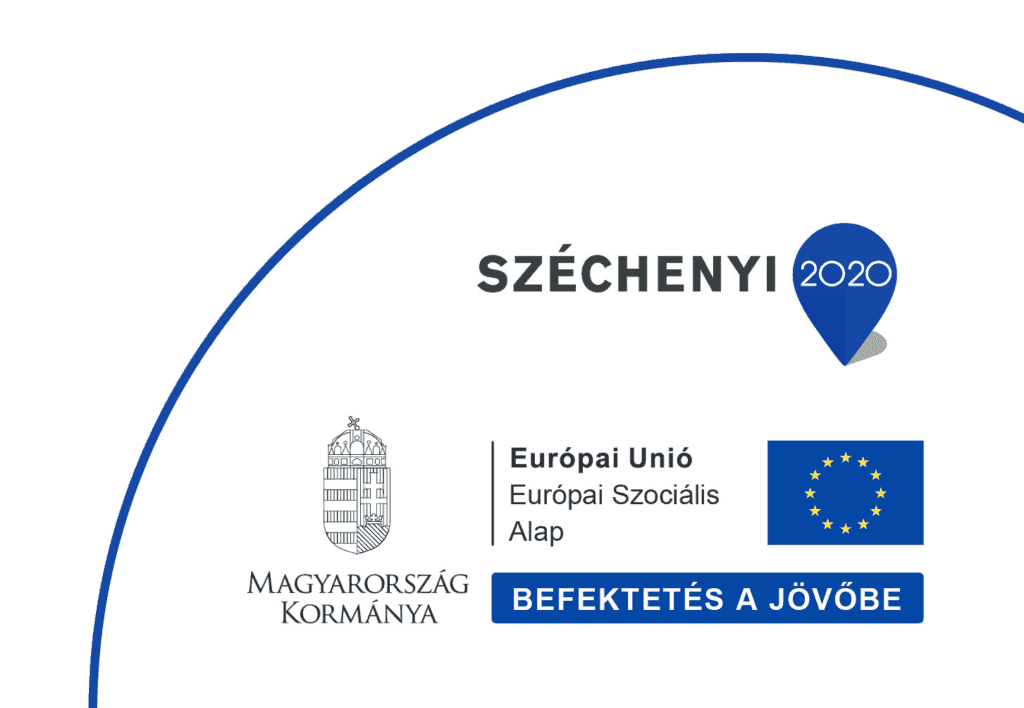
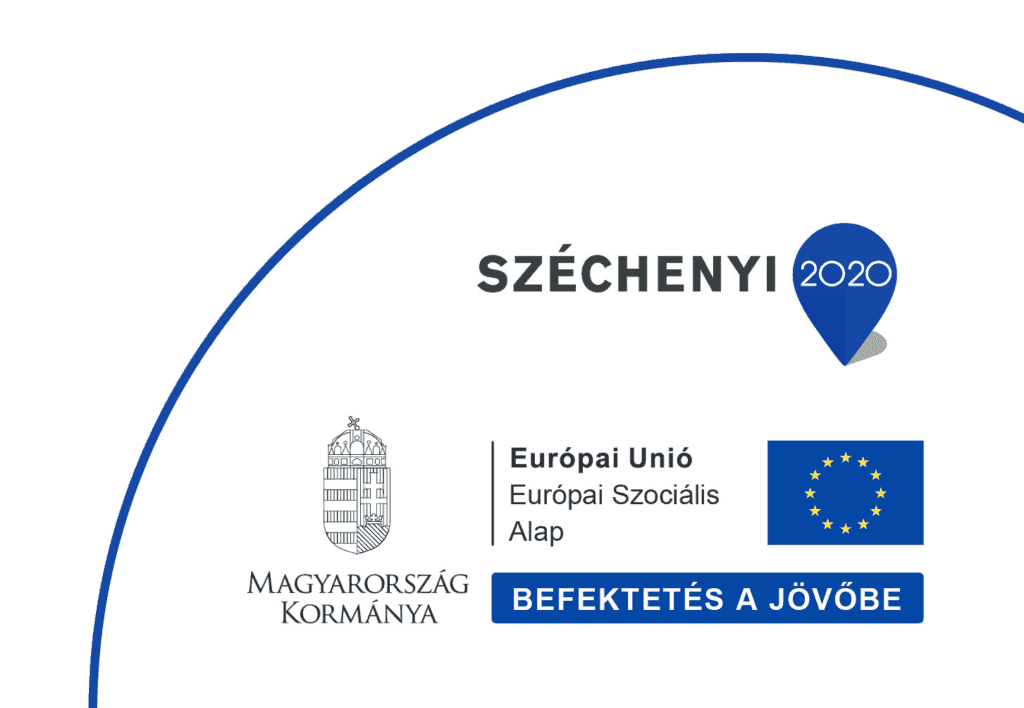